innovathermIhr kompetenter Partner für thermische Prozesse
Forschungsvorhaben Entwicklung von Brenntechnologien in Vorbereitung auf die Verwendung von Wasserstoff als nachhaltiger Brennstoff
Kompetenz und Begeisterung sind bei innovatherm seit jeher die Grundsteine für innovative Entwicklungen, die zum Erfolg und Wachstum unserer Kunden beitragen. Mit klaren Prozessen und motivierten Mitarbeitern sind wir ein verantwortungsvolles und flexibles Unternehmen. Als starker, zuverlässiger und kompetenter Partner unserer Kunden stehen wir für hochwertige Lösungen, Produkte und Dienstleistungen. In unseren zukunftsweisenden und nachhaltigen Ideen, die Maßstäbe setzen, begründet sich unser Erfolg.
Unsere Produkte und Leistungen
Nachhaltig in allen Facetten
Neue und bessere Produkte zu entwickeln, Fertigungsverfahren zuverlässiger zu machen sowie Energie und Materialkosten zu senken, all dies sind vorrangige Ziele der Innovationsaktivitäten keramischer Unternehmen und der Aluminiumindustrie. Innovatherm ist ihr zuverlässiger Partner, um Prozesse, bestehende Ofen-und Trocknungsanlagen mittels hochwertiger Technologien zu modernisieren und zu optimieren – für mehr Wirtschaftlichkeit und gute Umweltverträglichkeit bei niedrigeren Betriebskosten. Dafür setzen wir fortschrittlichste und eigens entwickelte Brennersysteme und Produkte ein.
Zum umfangreichen Liefer- und Leistungsspektrum der Innovatherm zählen:
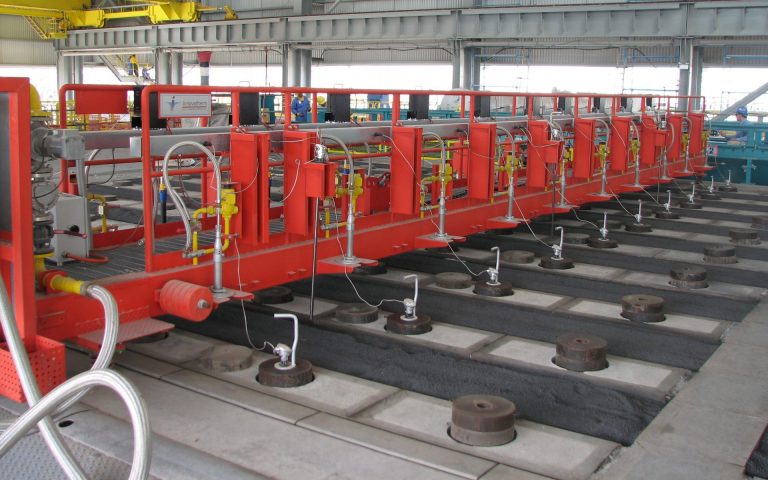
ProBake
Feuerungs- und Leitsystem für Anodenbrennöfen
Das innovatherm Feuerungssystem ProBake vereint 40 Jahre Know-how auf offenen und geschlossenen Brennöfen in einer einzigartigen Feuerungstechnologie. ProBake liefert den optimalen Ansatz für eine effiziente und ökonomische Führung von verschiedensten Brennöfen und setzt Maßstäbe in der Welt.
Die Regelungsstrategie basiert auf intelligenten Modulen und mathematischen Modellen, die auf die Basisregelung aufgesetzt werden, um eine optimale Produktion bei geringstem Energieverbrauch und Emissionen zu gewährleisten.
Mehr erfahren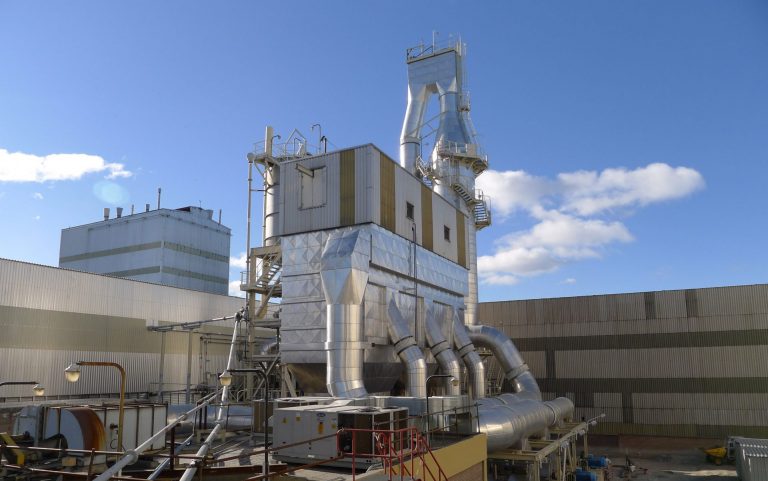
ProClean
Integrierte Rauchgasreinigunsanlagen für Anodenbrennöfen
ProClean beinhaltet eine mehrstufige Technologie zur maximalen Behandlung und Ab-Reinigung der Rauchgase aus dem Anoden Brennprozess – mit kontinuierlicher Rückkopplung an das ProBake Feuerungssystem. Die Struktur des Aufbaus ist abhängig vom Einsatzgebiet, der Umgebung und dem nötigen Reinigungsaufwand mit dem Ziel möglichen Umweltbelastungen vorzubeugen. Die Reinigung besteht im Wesentlichen aus Konditionierung (Quenchen), Ad- und Absorption und Filterung.
Mehr erfahren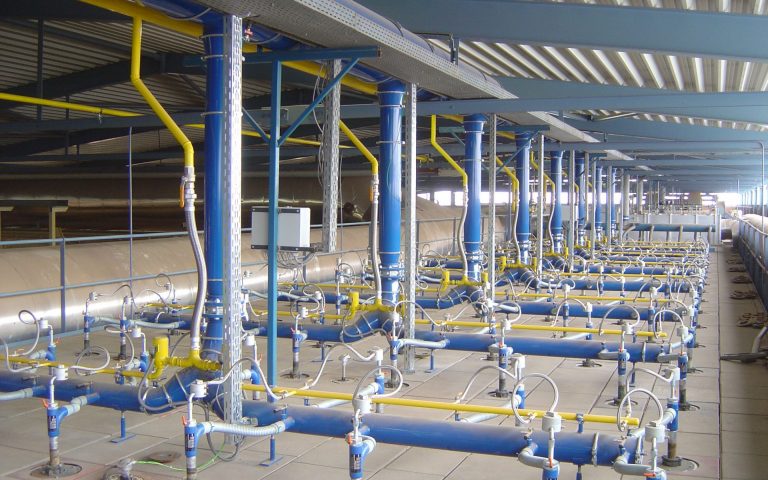
ProCeram
System-Lösungen für die grob-keramische Industrie
ProCeram umfasst die Produktfamilien novacontrol, novapuls and novajet für die keramische Industrie.
innovatherm ist heute – seit mehr als 25 Jahren – ein führender Anbieter von Prozessleitsystemen und Brennertechnologien für die Keramikindustrie.
Wir kennen die Komplexität und Abhängigkeiten des Produktionsprozesses. Wir berücksichtigen den Rohstoff, seine Aufbereitung, die Extrusion, Trocknung und Verbrennung. Wir verstehen den Prozess als Ganzes. Dieses geht über die Optimierung einzelner Regelkreise weit hinaus und liefert eine Gesamtlösung im Hinblick auf die gewünschten Produktparameter und Produktqualität.
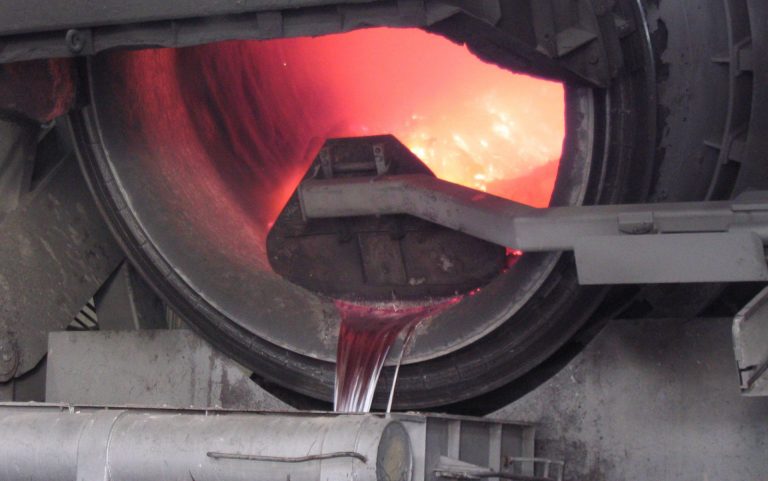
ProCast
Produktionssteuerung in der Giesserei
ProCast ist ein skalierbares Leitsystem zur Chargenplanung, automatischen Berechnung der Chargenzusammensetzung und Chargierung in Sekundär- oder Primär-Gießereien. Chargenplanung, Chargenberechnung sowie Gattierungs-Berechnung und das damit zusammenhängende Verwiegen sind in einzelne Automatisierungsstrategien integriert, um hohe Produktivität und Zuverlässigkeit bei gleichzeitig hohem Qualitätsstandard und niedrigen Produktionskosten sicherzustellen. ProCast berechnet bestmögliche Chargen für die gewünschten Ziellegierungen unter Berücksichtigung niedrigster Materialeinsatzkosten. Die aktuellen Preise können über eine Remoteverbindung abgefragt werden. Zusätzlich kann ein komplettes Materialfluss-Verfolgungssystem auf Basis eines WiFi-Funknetzwerks implementiert werden.
Mehr erfahren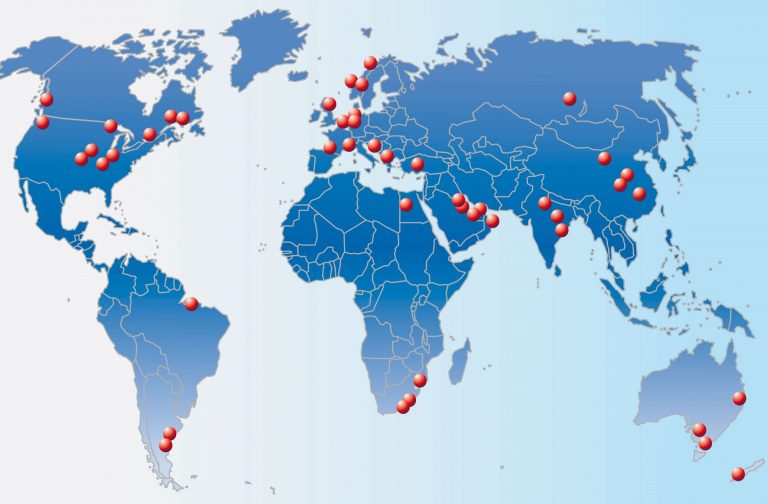
Unsere Referenzen
Weltmarktführer für Feuerungen auf Anodenbrennöfen
innovatherm hat sich zum Weltmarktführer für Feuerungs- und Prozessleitsysteme auf Anodenbrennöfen entwickelt. Bis zum heutigen Tage sind mehr als 230 Produktionsfeuer auf über 90 verschiedenen Anodenöfen im Einsatz.
Mehr erfahren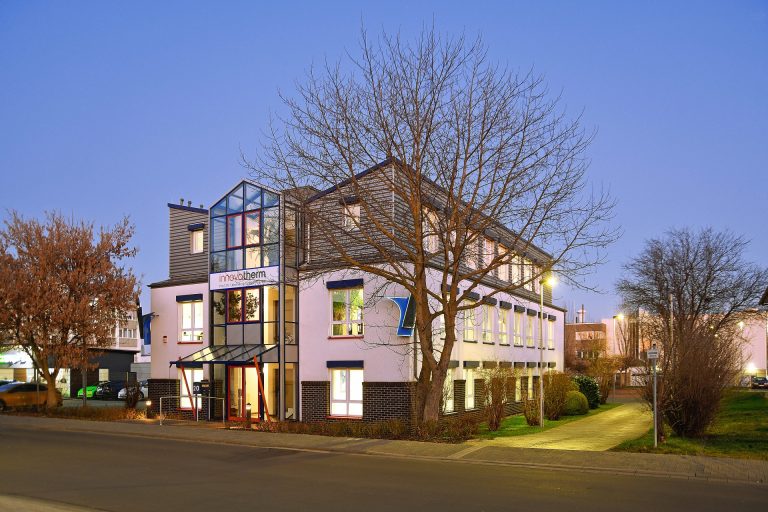
Unser Service Angebot wird durch folgende Leistungen ergänzt
- Beratung
- Prozessanalyse sowie Prozessoptimierung
- Modernisierung bestehender Feuerungssysteme
- Installations- und Inbetriebnahmeüberwachung
- On The Job und Class Room Training
- Umfangreicher After Sales Service
- Ersatzteillieferungen